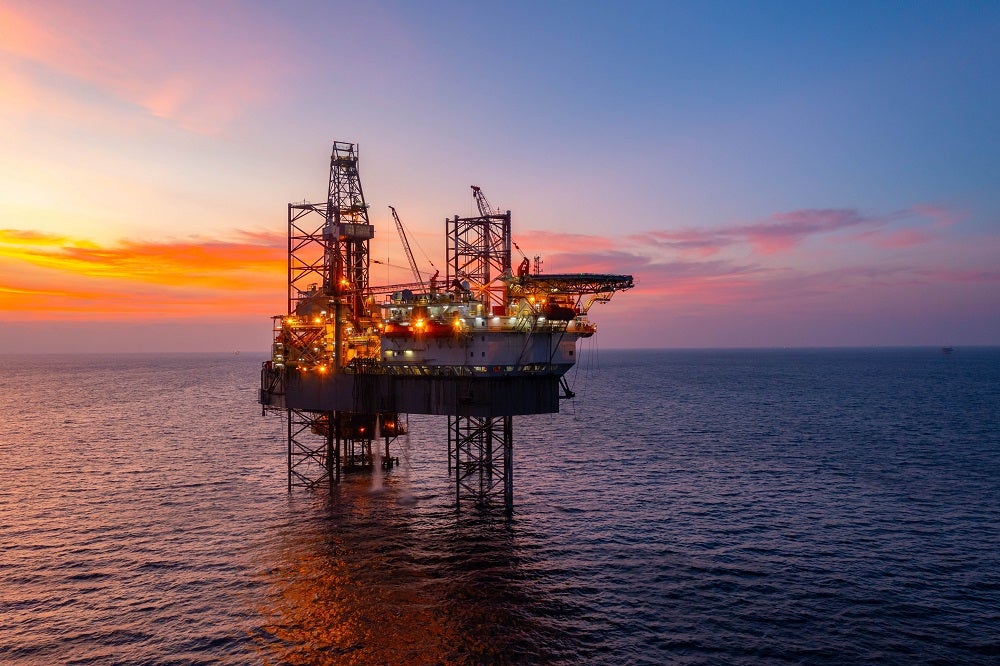
Hydraulic systems are indispensable for many offshore operations, from oil and gas drilling rigs to wind turbines and offshore supply fleets. These systems power essential equipment, enabling the smooth operation of vital tasks such as drilling, lifting, and turbine blade control. However, the harsh offshore environment exposes hydraulic cylinders to corrosive saltwater, high pressures, and extreme weather conditions, leading to frequent breakdowns and costly repairs.
Hydraulic failure not only impacts operational efficiency but can also lead to significant safety risks.
Financial impact of hydraulic failure in offshore operations
In offshore industries, unplanned downtime due to hydraulic system failure can be catastrophic. When a hydraulic unit breaks down, it halts key operations, whether on an oil rig, a supply vessel, or a wind turbine. Each hour of downtime represents lost productivity and revenue. For example, in oil and gas drilling, where thousands of flexible hose assemblies and hydraulic fittings are critical to operations, a single failure can cause severe delays in production.
According to a 2022 GlobalData Predictive Maintenance in Oil and Gas report, unscheduled downtime due to ineffective maintenance practices can cost global oil refiners an additional $60 billion annually. Offshore rigs, often located far from shore, face even more significant challenges, as replacement parts and specialised technicians must be flown in at high costs, delaying repairs further. For wind farms, particularly those offshore, the logistical difficulty of accessing turbines in the middle of the sea compounds the problem.
The solution lies in preventative maintenance, a strategy that mitigates these costs by detecting potential issues before they lead to catastrophic failure. It relies on regular monitoring and data gathering to assess equipment wear and tear, allowing operators to schedule repairs at convenient times and avoiding costly breakdowns.
‘Deceptively simple solution’
In the case of hydraulic systems, Fluid Control Services, based in the US, provides a deceptively simple solution with Seal Saver, a custom-fitted protective boot designed to shield hydraulic cylinders from the harsh offshore environment.
“Saltwater is particularly harsh on hydraulic cylinders, causing corrosion and frequent breakdowns. Our ballistic nylon boots have been shown to last up to a decade, even in marine environments,” says Leigh Carlson, CEO, Fluid Control Services. By protecting cylinders from corrosion and debris, Seal Saver extends equipment life and reduces maintenance costs significantly.
Safety considerations in offshore hydraulic maintenance
Offshore environments pose not only financial risks but also safety hazards. Equipment failure can result in dangerous situations, putting workers at risk of injury. Hydraulic systems are critical to the operation of cranes, winches, and turbines, and failure in any of these systems could lead to catastrophic consequences. In oil and gas operations, a malfunctioning hydraulic system could result in uncontrolled releases of oil or gas, creating an environmental disaster in addition to safety risks for workers.
In this high-risk environment, preventative maintenance is essential to ensure operational safety. GlobalData’s report highlights predictive technologies such as vibration monitoring and thermography, which have become integral to offshore operations, allowing for the early detection of equipment wear and tear. These technologies help to identify issues before they escalate into dangerous failures. In combination with protective solutions such as Seal Saver, preventative measures can drastically reduce the likelihood of accidents and environmental harm.
Fluid Control Services has extensive experience in this area, working closely with clients in the offshore sector to protect critical hydraulic equipment. Carlson explains: “The harsh conditions offshore, including high pressure, salt exposure, and corrosive elements, make it crucial to protect hydraulic systems proactively. Seal Saver is a key part of ensuring that hydraulic cylinders remain operational, avoiding dangerous failures that could jeopardise worker safety.”
The role of hydraulic systems in offshore wind farms
Hydraulic systems play a pivotal role in wind energy, particularly in controlling the movement of turbine blades. Offshore wind farms are exposed to some of the harshest elements, including salt spray, high winds, and fluctuating temperatures. Over time, these conditions can wear down hydraulic cylinders, causing pitch system failures that can result in downtime or even turbine damage.
Offshore turbines are especially difficult and costly to repair due to their remote locations. This makes preventative maintenance even more critical in wind energy operations. Hydraulic systems must be protected from the corrosive effects of saltwater and other environmental factors to ensure reliable operation. Seal Saver’s protective boots, made from durable materials like ballistic nylon, are designed to withstand these extreme conditions, ensuring that hydraulic systems last longer and operate more efficiently.
Carlson highlights the growing importance of preventative maintenance in the renewable energy sector: “Offshore wind is an expanding industry, and maintaining the efficiency of these turbines is key to meeting energy demands. Seal Saver helps ensure that pitch cylinders remain in optimal condition, preventing costly repairs and downtime.”
Why preventative maintenance is a business imperative
In offshore industries, the stakes are high. Whether in oil and gas, offshore supply fleets, or wind farms, hydraulic systems are essential to the smooth operation of critical equipment. The financial and safety risks posed by hydraulic failure cannot be overstated, but with preventative maintenance strategies, companies can protect their assets, improve operational efficiency, and ensure worker safety.
Fluid Control Services, through its innovative Seal Saver solution, offers an effective way to safeguard hydraulic cylinders from the harsh offshore environment. By preventing corrosion, debris build-up, and mechanical wear, Seal Saver extends equipment life, reduces downtime, and ultimately saves companies money.
For offshore operators looking to protect their investment and enhance safety, implementing a robust preventative maintenance plan, including reliable solutions like Seal Saver, is a business imperative. Download the whitepaper below to find out more.