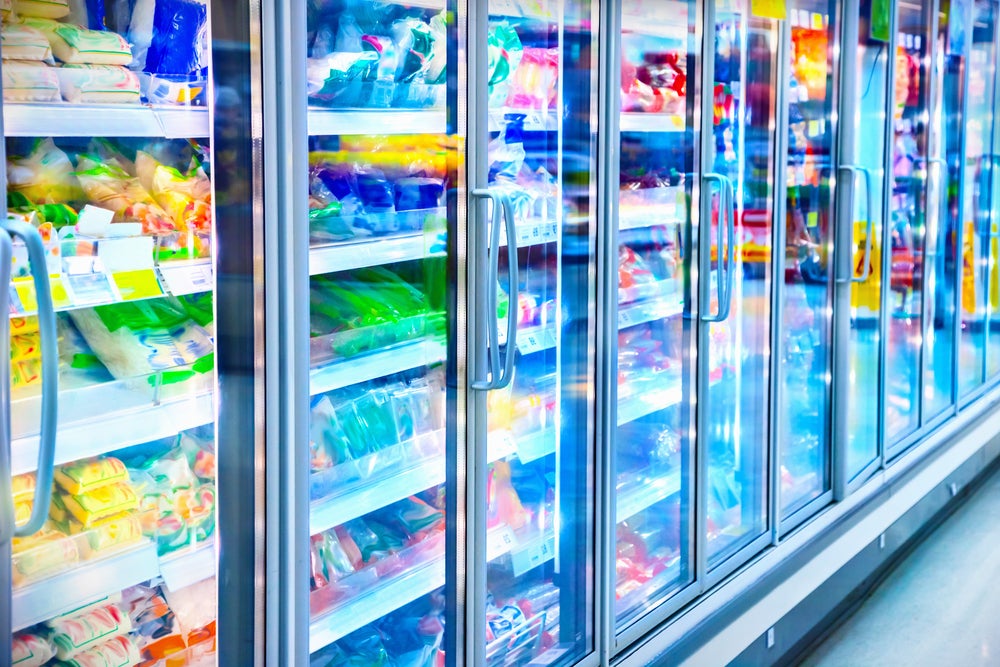
Household and commercial appliances like refrigerators and air conditioners are notorious for their climate footprint. Research commissioned by the UK Government has found that refrigeration is the largest source of energy in a supermarket, accounting for up to 60% of the total electricity consumed annually. Meanwhile, a few years ago, the International Energy Agency (IEA) published a report warning about a blind spot in the energy debate – a fast increase in electricity consumption to power the rapidly growing demand for air conditioning units, especially in parts of the world where global warming is already causing disruption and discomfort to everyday life.
The IEA finds that air conditioners and electric fans account for about 20% of the electricity used in buildings worldwide or 10% of all global electricity consumption. The world’s energy watchdog expects energy use for residential air conditioning to increase by 280% by 2050 if the status quo continues.
Appliance manufacturers are having to reconsider the material and chemicals they use to meet strict new rules governing their environmental impact. These include the European Union’s phasing out of fluorinated (F) gases, a milestone part of the EU’s Green deal.
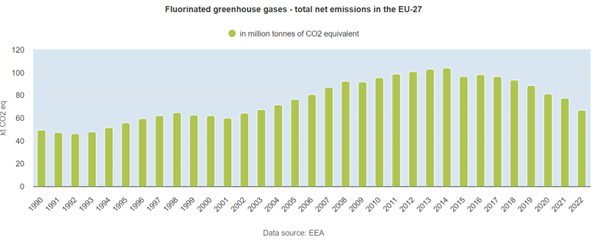
A landmark new report by the market intelligence firm GlobalData designed to be used by businesses to assess and improve their environmental, social and governance (ESG) performance, notes: “Numerous companies all over the world are hurriedly adapting their operations and supply chains to manage an influx of new ESG-related regulations. This includes mandatory ESG reporting, emissions pricing, and laws governing supplier due diligence.
“CEOs who do not take a forward-thinking approach to mitigating ESG risks will face the wrath not only of regulators, but also investors, lenders, customers, suppliers, and employees. Forever responding to the next regulatory deadline, they will find themselves constantly on the back foot, failing to properly strategize for the longer term.”
Getting ahead of compliance
To get on the front foot and prepared for a new operating environment, the heating, refrigeration and air conditioning (HVACR) industries must take bold measures to reduce emissions and embrace better environmental stewardship. This is where, Alleima StripTech believes, innovation in compressor valve steel can help.
Alleima has recently published an academic paper on its research findings into how novel compressor valve technology can play a significant role in setting new energy efficient standards governing appliances and in 2024 launched the latest offering in its Freeflex® product line, Freeflex® Versa – what it describes as a pioneering compressor valve steel.
Alleima says it has been engineered to enhance fatigue properties as well as allow for the design of smaller, more energy-efficient compressors because of its superior microstructure and mechanical properties. It is specifically tailored for household, commercial and industrial refrigeration and freezer applications.
Engineering excellence
Alleima says Freeflex® Versa builds on the success of its predecessors, Hiflex™ and Freeflex® Core. It offers improved mechanical properties, including impact and bending fatigue resistance, residual stresses, and wear resistance. This martensitic, stainless-steel product is designed to meet the rigorous demands of high-end HVACR applications. Its enhanced properties enable the development of smaller, lighter compressors with more complex valve geometries, crucial for advancing energy efficiency and the miniaturisation trend in compressor technology.
According to Alleima, Freeflex® Versa’s exceptional fatigue resistance and elevated wear resistance create ideal conditions for managing future compressor demands. These improvements contribute to higher reliability and increased Coefficient of Performance (COP), essential metrics for efficient refrigeration and freezer systems.
Anders Hoel, senior research engineer at Alleima, emphasises the significant impact of even the smallest component in an appliance: “Our premium compressor valve steel provides increased design freedom, leading to more energy-efficient appliances and sustainable products.”
Over the past decade, Alleima has been at the forefront of advancements in compressor valve steels, consistently meeting the latest energy efficiency standards across diverse HVACR applications. The introduction of Freeflex® Versa represents a substantial leap forward, building on extensive research and development efforts. By enhancing fatigue properties and supporting the design of more energy-efficient compressors, Alleima is helping to shape a more sustainable future.
To find out more about Alleima StripTech’s compressor steel product line, Freeflex®, including the new Freeflex® Versa, download the whitepaper below.