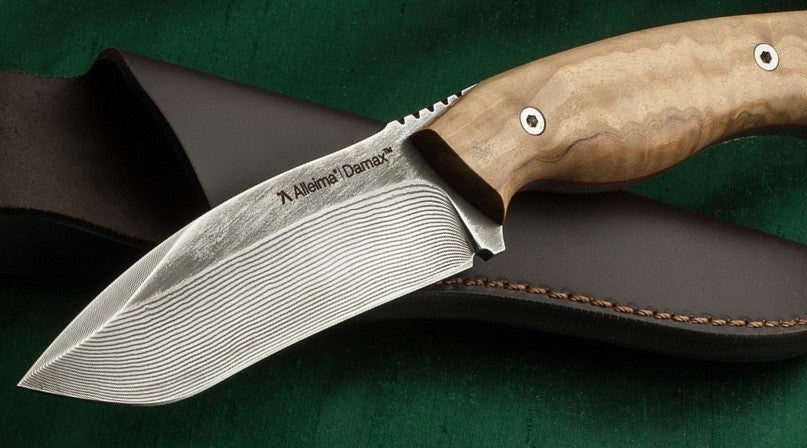
Damax™ by Alleima presents an opportunity investment in Damascus steel products, as Alleima marks the introduction of the first mass-produced Damascus steel blades to the market.
An exceptional steel, Damascus has always been the preserve of the very top end of the knife market. It is typically handcrafted on a small scale using a complex manufacturing process that dates back to the Samurai and Viking warriors. Arabs introduced the Indian wootz to Damascus for swords as far back as the third century.
Damascus steel knives are renowned for their functionality, ductility and hardness, as well as their aesthetic appearance. The distinctive patterns running across their surface are the result of multiple layers of steel from at least two different grades that are repeatedly heated and folded.
Now Damascus steel is available in large, repeatable quantities for the first time after Alleima in partnership with Balbachdamast found a way to produce the steel through large-scale manufacturing.
Here, Paul Favell, global strategic business development manager at Alleima explains why the firm, a steel innovator for 100 years in Sandviken, Sweden, has focused recent R&D efforts to scale up Damascus steel production and how it can manage to protect the quality of the multi-layered Damascus through the industrialised manufacturing process.
Firstly, Paul, could you tell us a bit about Damax™ by Alleima?
Paul Favell (PF): Damax™ is our trademark for the Damascus steel we are producing in partnership with Balbachdamast GmbH & Co. KG, one of the most well reputed names in Damascus forging worldwide. Damascus steel is made by forging at least two different steel grades together, creating a true metallic bond between them. By combining the two grades; a third grade is born; Damax™. By finishing and etching, a unique pattern appears.
The steel grades in Damax™ are Alleima® 7C27Mo2 and Alleima® 19C27. The new grade Damax™is perfectly suited for knife applications both for the kitchen and the outdoors. Damax™ Damascus steel has up to 135 layers of martensitic stainless.
The material can be heat treated to more than 60 HRC and with the fine microstructure and chemical analysis it offers excellent corrosion resistance, and very sharp edge capability. The product is supplied in a stack of 7c27mo2 and alternate 19c27 and this allows customers to either produce a knife with the layers clearly visible or they can emboss with their own unique patterns. With our partner Balbach we now have repeatable material on an industrial scale. From the hot rolled strips we can roll any thickness dimension below 4.2mm and made to customer requirements.
Why focus on Damascus steel?
PF: At Alleima we are renowned for developing new knife materials. Since we launched our very first knife grade over 100 years ago, we have developed 10 well-known grades, the latest being Damax™. The knife market enjoys new products and interest in new steels, like our Damascus steel, has been growing. We believe that demand will continue to increase. We realise the demand and have the capabilities and excitement to make it happen. Our industrialised technique makes the production process more cost efficient on a large scale with repeatable quality and ideal to serve a wide market.
Why has it not been possible to offer the knife market this steel technology previously?
PF: It takes expertise, investment, and capability that Alleima and Balbach bring together. To produce such a product on an industrial scale has taken years of research and trials to master the production process. Having integrated R&D, melting, hot rolling, cold rolling and the finishing has allowed us to fully control all the process and metallurgy and to make sure we maintain the product quality.
Why should kitchen knife makers be switching to Damax™ by Alleima in 2024?
PF: Our Damax™ is all stainless. The fine microstructure allows the product to be high polished, easily resharpened, with razor sharp edges and good toughness. We have seen some of the most beautiful kitchen knives out of our Damax™ material, non-embossed and embossed, allowing customers to put new high-quality products to the market.