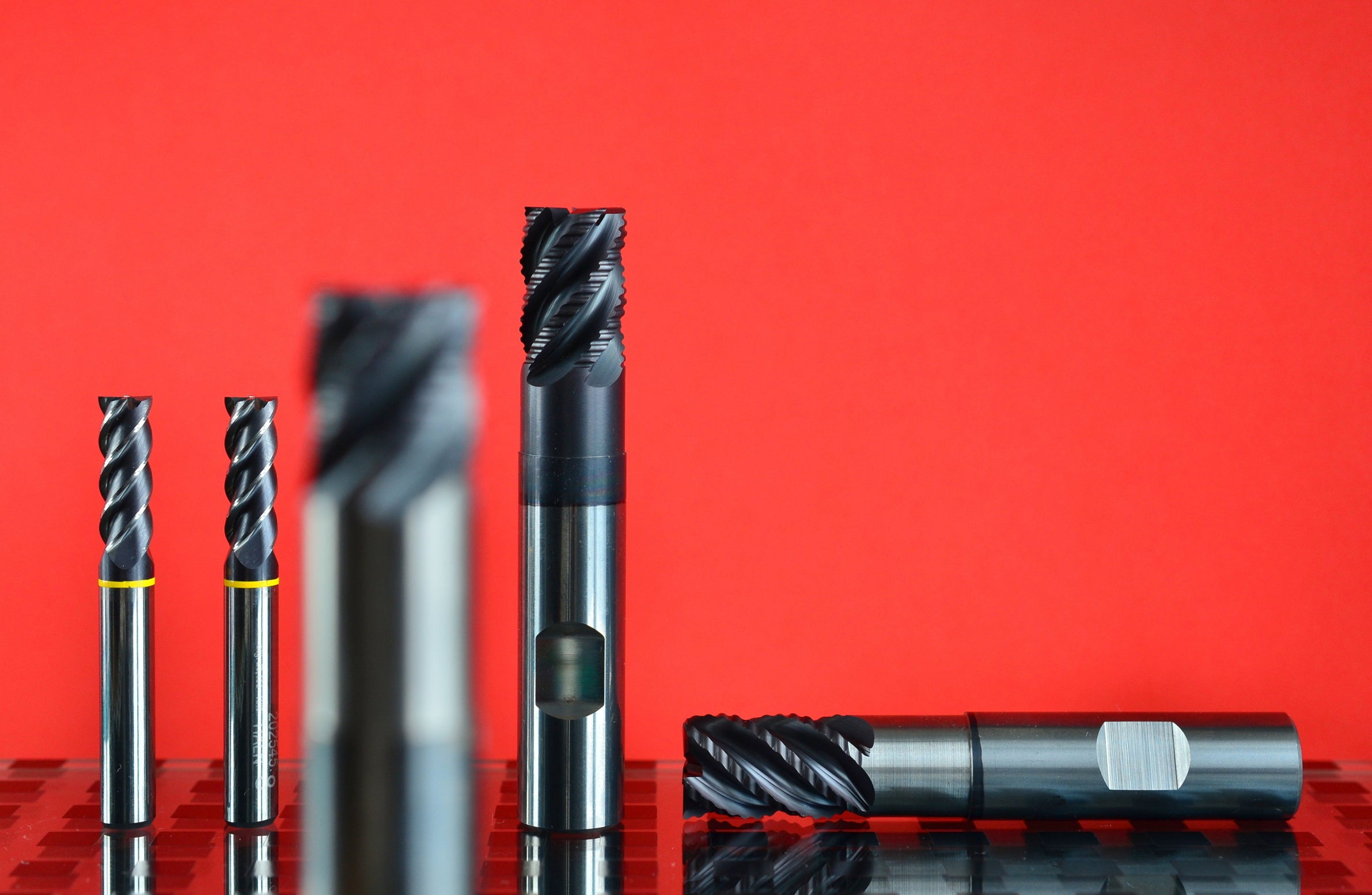
There are thousands of reasons why coatings get applied. But there is one thing they all have in common: The coating must meet the highest quality requirements to fulfil its function – whether visually or as wear protection.
Equipment that is not capable of creating the necessary environmental conditions prevents the best possible economic benefit.
The big questions are: how can a good quality of the coating be ensured? And what can maintenance do to prevent costly failures?
Care work for best practice coating results
PVD and CVD machines get thoroughly tailored to the application, ensuring the right vacuum equipment for the process is being deployed. They are delivered together with the system operating instructions. As most plant operators wish to see long service intervals, you would think at least basic maintenance activities get carried out. Unfortunately, however, the general understanding of service work around the hardware is perceived to be the sole responsibility of maintenance.
Everyone who contributes to the process ultimately has an influence on the coating’s quality: those responsible for the purity and dryness of the targets, those loading and unloading the equipment and those who maintains it. Cleanliness, for example, is an important issue that everybody is responsible for. In an environment that is not necessarily clean, it is nevertheless and precisely for this reason of extraordinary importance to have an eye for detail. It is important to develop routines such as wiping the door seals and keeping doors closed when no load is being brought in or out.
Yannick May is an application engineer at Pfeiffer Vacuum. He describes different levels of service work and who should perform them to gain best practice coating results, using another example reflecting the importance of cleanliness: “With each layer of coating that we apply, we not only coat the parts and surfaces we intended, but also parts and surfaces of the equipment itself. These unintentional layers build up over the runs to form a kind of sponge, resulting in a very large surface area.” This can create issues with pump down rates and achieving process pressure, as moisture comes into the chamber every time the door gets opened, and deposits in the sponge-like areas. “To properly clean a chamber” May explains, “remove the shielding and do not forget the areas behind them”.
Basis for a good vacuum for PVD/CVD
No PVD or CVD process works without vacuum; the pressures range varies from 10-4 hPa up to 10 hPa depending on the coating type. To achieve this, the actual maintenance work itself has to become carried out conscientiously. And following a checklist before handling the equipment back over to production is vital.
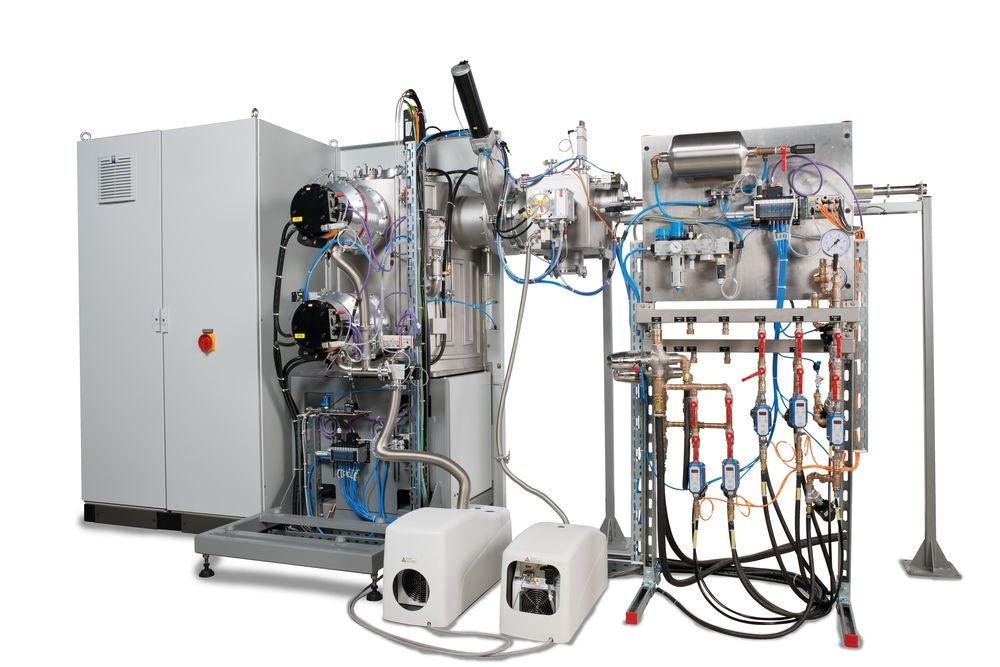
After maintenance, especially when parts have been replaced, it is not uncommon for leaks to occur, even on existing equipment. The causes are often forgotten or may be due to defective seals and joining errors. To find these leaks the proper use of helium leak detectors is essential. Operators must be aware that not every issue with pump down times is caused by leaks. “For example not only leaks, but also the outgassing from even a single fingerprint inside the chamber has a measurable influence”, explains May. This is why operators, maintenance and everybody else working with the parts to be coated or the equipment used to coat them must wear gloves at all times.
Yannick May’s top 3 tips for coaters:
- Everything that enters the chamber, is a seal or a sealing face must meet highest standards of cleanliness. Otherwise the pump down rates are extended.
- Proper craftmanship includes leak checking the entire system before handing the equipment back over to production.
- Leave nothing in the chamber that does not belong there, no objects and also no fingerprints.
Experience shows that there are different causes for excessively long times leading up to process pressure being reached. May notes that drifting gauges – or those that are not screened off during the coating process – can also cause errors. This explains why counting on the expertise of a company like Pfeiffer Vacuum and asking for support is the best way to accumulate knowledge while avoiding investing time and money into an individual learning curve.
A helping hand is never far away thanks to Pfeiffer Vacuum’s knowledge. Wherever you’re unsure in the wear protection workstream – whether it’s defining and implementing appropriate maintenance procedures, finding the right vacuum conditions for a particular coating, assisting with troubleshooting, or something else entirely – Pfeiffer Vacuum can support and advise you.
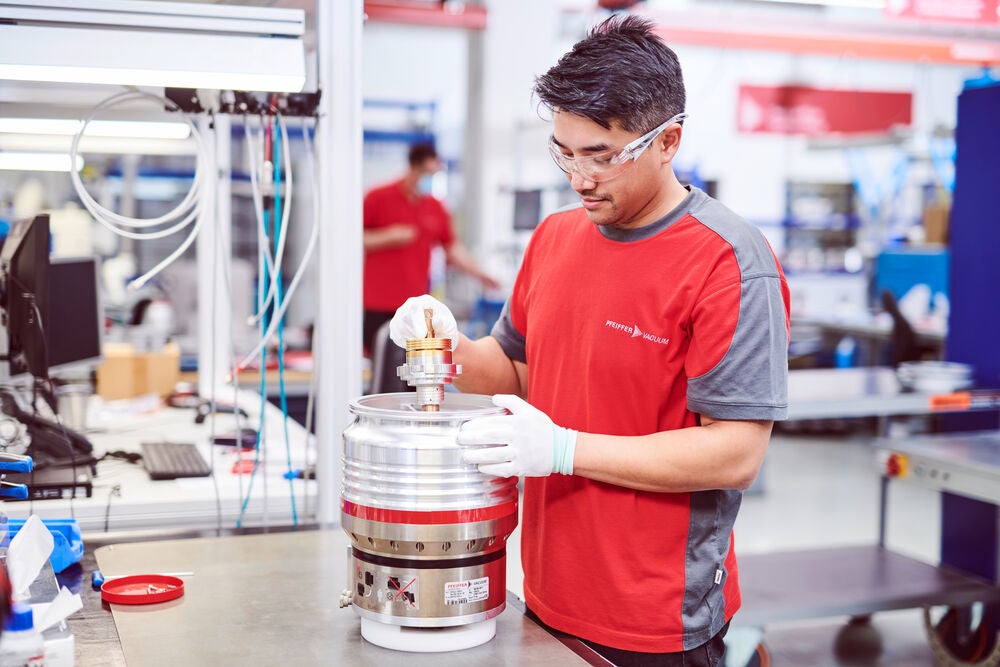