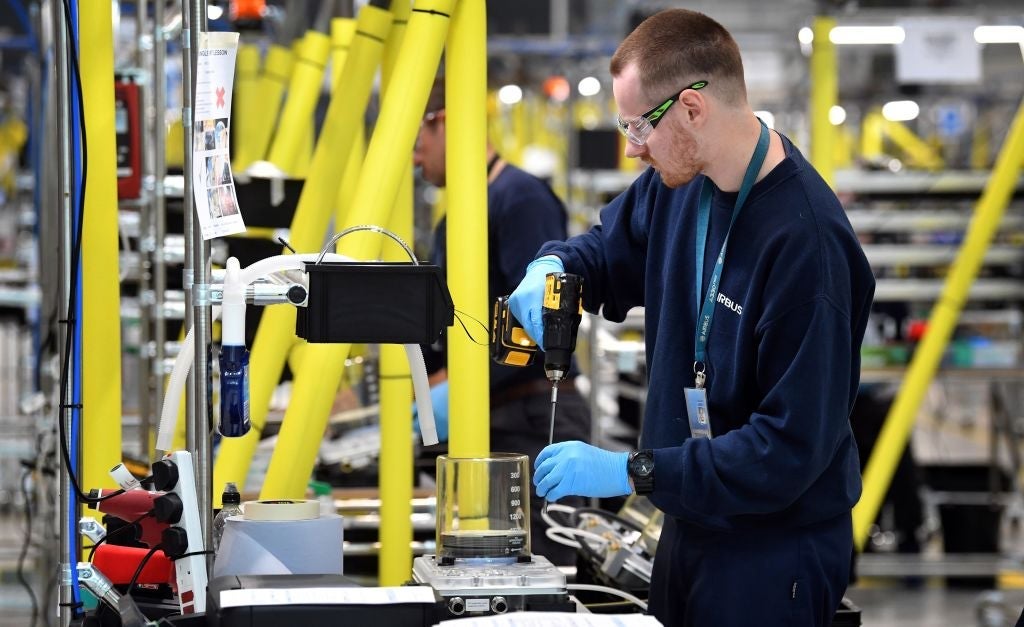
With the combined blow of Brexit and Covid-19 dominating news cycles for the past year, the fate of the manufacturing industry has featured prominently in numerous headlines. However, according to experts across the UK (and the US), the biggest issue facing the industry isn’t Brexit or even Covid-19, although both pose significant threats – it is skills.
For the UK, there are a number of factors aggravating its skills gap. Stephen Phipson, the CEO of Make UK, highlights an ageing workforce as a key issue. “More than 50% of our manufacturers will always cite the fact that their workforce is aged 50-plus as a leading concern on the skills side,” he says. “They are worried about retirement looming and not enough people filling the hopper on the other side, and we have to ask ourselves why that is.”
According to figures from the World Bank (as detailed in the graph above), the UK is ranked third for attracting talent and sixth for retaining it. Whereas other manufacturing leaders such as Germany, China, the US and Switzerland hold a better balance between the two.
With Brexit minimising the free movement of workers from Europe, the pool of talent the UK can attract is set to diminish, making the issue of a skills gap more prominent.
Isn’t it a rubbish job?
For the UK, manufacturing is intertwined with the history of many of its prominent cities and towns. From shipbuilding to carmaking to food and drink, manufacturing hubs have played an integral part in boosting the UK’s industrial output and enhancing its global reputation. Why then, for an industry that has played such a big part in painting the legacy of Great Britain, is there such a misunderstanding and stigma around jobs in manufacturing?
How well do you really know your competitors?
Access the most comprehensive Company Profiles on the market, powered by GlobalData. Save hours of research. Gain competitive edge.
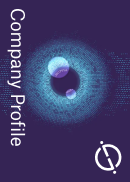
Thank you!
Your download email will arrive shortly
Not ready to buy yet? Download a free sample
We are confident about the unique quality of our Company Profiles. However, we want you to make the most beneficial decision for your business, so we offer a free sample that you can download by submitting the below form
By GlobalDataMany people outside of manufacturing have an old-fashioned view of it as a dirty, oily business, but if you go into a modern manufacturing plant, they are pristine, and it is a very high-tech process. David Bailey, Birmingham Business School
For many, the perception of manufacturing jobs is that of ‘unskilled labour’, conjuring up images of grimy factories sitting under chimney smoke. Parents, given the choice, are more likely to opt for their offspring to go into what they consider to be more academic fields.
However, when looking at the future of manufacturing, this perception couldn’t be farther from the truth. It is wrong not only in the context of modern manufacturing, but also in terms of what the industry will evolve into.
David Bailey, a professor at Birmingham Business School and a senior fellow for the UK within the Changing Europe programme, explains. “Many people outside of manufacturing have an old-fashioned view of it as a kind of dirty, oily business, but if you go into a modern manufacturing plant, they are pristine, the floors are very clean, and it is a very high-tech process,” he says.
Phipson agrees, saying: “Many parents have this image of Victorian industrial sites, old factories and smoky smokestacks – it is not like that at all. There is a lot of work to do around encouraging youngsters into the profession.”
Bailey highlights Germany’s approach to using education to support the development of its manufacturing industry. “We have had a policy in the UK of trying to encourage people to go to university, which is fine, but there really wasn’t an alternative,” he says. “Whereas in Germany, it is very clear that there is this long-term alternative that exists, which is valid, which is highly respected. It is supported by the government through its educational policies, so that is hugely important for encouraging young people into manufacturing.”
Industry 4.0 accelerates need for skills
It isn’t just an ageing workforce or reticence among younger workers that is behind the scarcity of manufacturing talent. Industry 4.0 and the rise of automation in advanced manufacturing has created new, advanced job roles and a need for consistent innovation in the industry. A balancing act of implementing innovative practices with investing in training skilled workers to carry out those practices is crucial, and not just for the advancement of the UK’s manufacturing industry, but for survival.
Bailey says: “There is a lack of understanding of how skilled it has actually become, and that is only going to change even more in the future with the development of industry 4.0. It is going to require even more upskilling of the labour force.”
Generally, upskilling is being highlighted as something that should be a key priority on a global scale. The World Economic Forum released a report on 25 January 2020 in partnership with PwC entitled Upskilling for Shared Prosperity.
The report states that wide-ranging investment into upskilling could boost global GDP by $6.5trn by 2030. Furthermore, when testing an accelerated scenario – one that would see the skills gaps closed by 2028 – industry 4.0’s impact on job creation within manufacturing proved to be an important driver. As much as 38% of the additional GDP that would be gained could be attributed to upskilling in the business services and manufacturing sectors.
This highlights the urgent need for effective upskilling programmes alongside attracting new talent to the industry. The report goes on to predict that up to 45% of jobs in manufacturing could be automated by the end of the 2030s. It is important to understand that a job becoming more automated does not alleviate the need for human workers. What it does is heighten the need for skilled workers that possess critical thinking and programming skills; automation minimises lower-skilled manufacturing jobs.
There is, however, a concerning trend in the UK that is seeing manufacturing jobs deplete. This is trend is also occurring in the US, alongside a growth in gross value added (GVA) that the UK is also mirroring. Yet, where the US is beginning to see an improvement in its manufacturing employment, the UK still suffered a decline into 2018.
Isn’t manufacturing dying anyway?
The idea that UK manufacturing is a dying industry – and therefore irrelevant and unstable as a career path – is a reputational obstacle to overcome.
“Until relatively recently, the view among many policymakers was that most manufacturing would simply disappear,” Bailey explains. “It was not valued at all. If we were not going to have a competitive future in, say, car assembly or aerospace, their view was that it would just shift overseas.”
We need a longer-term industrial strategy in the UK. We don’t really have that at the moment. There seems to be some reluctance in this government to do an industrial strategy, but that is the way you put all these pieces together. Stephen Phipson, Make UK
Although manufacturing’s GDP percentage in the UK has dropped from its glory days of approximately 30% in the 1950s to approximately 10% in 2021, it has been steadily rising since 2009. This rise could be attributed to lessons learned in the aftermath of the 2008 financial crash.
Bailey continues: “In the wake of the global financial crisis [the UK government] realised that maybe we had become overdependent on financial services, real estate and retail. Countries such as Germany, which had a balance of payment surplus and a big manufacturing sector, actually recovered more quickly.”
At the beginning of 2021, the UK manufacturing industry ranks ninth globally in manufacturing output and tenth in terms of global exports. So, although UK manufacturing is suffering at the hands of Covid and Brexit, it would be wrong to consider it dead or dying.
Furthermore, the UK is consistently rated highly for innovative manufacturing, with the graph above showing that it scored impressively in the World Bank’s GCI index, although it struggled to keep up with other industry leaders such as the US, Switzerland, Germany and China for GVA percentage.
What industrial policy?
UK manufacturing is in dire need of a strategy, support and investment. The UK government would be well advised to offer potential investors and businesses a clear five-year plan to provide some stability post-Brexit. This is particularly important for manufacturing, as investments are usually very long-term projects and do not typically have the autonomy to be agile or reactive to circumstance.
Furthermore, upskilling and reskilling must be a priority, especially now that the UK’s unemployment rate is rising in the wake of the Covid-19 pandemic. With rising protectionist and nearshoring trends set to continue in 2021, plus many businesses rethinking their supply chains, the UK could miss a trick if it doesn’t up its talent offering to attract these investors.
The UK government has a history of window dressing when it comes to its industrial policy roll-outs. If the country is to remain in the top ten globally for manufacturing output post-Brexit, more must be done to encourage young people into the industry and to flip perceptions in older generations.
Phipson agrees. “We need a longer term industrial strategy,” he says. “We don’t really have that at the moment. There seems to be some reluctance in this government to do an industrial strategy, but that is the way you put all these pieces together.
“Without that plan, without that ability to scale up and get the right skills in, the impact is that investment is low, because people can’t see what the future will look like. We have seen big, big fall-offs in investment. We need an overall plan and an integral part of that is skills, because skills is the number one issue for manufacturing.”