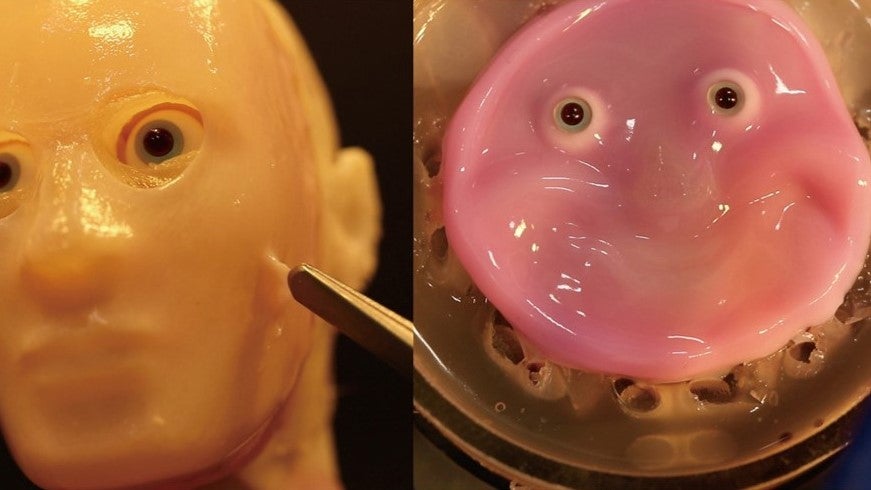
Having existed since the WABOT-1 was completed in 1972, humanoid robots are a rapidly developing sector – but the ‘human’ aspect has struggled to move from theory to reality.
Led by Professor Shoji Takeuchi, a team at the University of Tokyo is looking to change this and has made progress in the attachment of engineered skin tissue to robotic surfaces, using V-shaped perforations to bind the material to complex structures.
It is hoped that realistically attached skin might herald a new era for humanoid robots, and subsequently contribute to medical developments, offering potential in robotic mobility, self-healing, sensing capabilities and lifelike appearances.
Developing skin for humanoid robots
Looking to attach engineered skin tissue realistically, the team used “perforation-type anchors” inspired by human skin ligaments.
They used a living skin model composed of cells and extracellular matrix, described as having “the potential to be an ideal covering material for robots due to its biological functionalities.”
Holding the skin close to the surface, the team fed a collagen gel into a series of carefully engineered minuscule V-shaped perforations. The gel is naturally viscous, so the team used a water-vapour-based plasma treatment – a common technique for plastic adhesion – to improve the gel’s penetration in the perforation structures.
How well do you really know your competitors?
Access the most comprehensive Company Profiles on the market, powered by GlobalData. Save hours of research. Gain competitive edge.
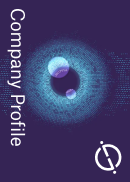
Thank you!
Your download email will arrive shortly
Not ready to buy yet? Download a free sample
We are confident about the unique quality of our Company Profiles. However, we want you to make the most beneficial decision for your business, so we offer a free sample that you can download by submitting the below form
By GlobalDataThe team demonstrated the method in two applications – by constructing a three-dimensional skin using a still facial mould covered with the skin equivalent and by actuating the dermis on a robotic ‘face’, which moved to create a ‘smile’.
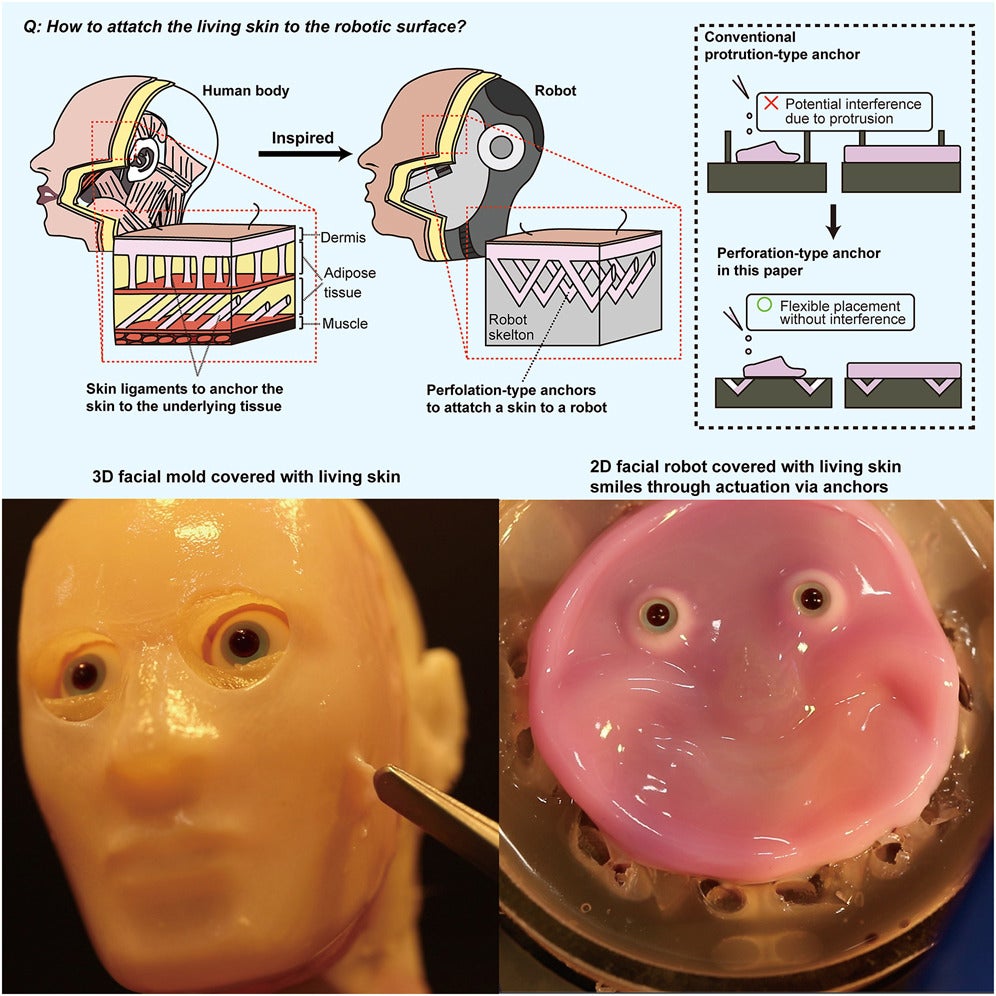
Previous methods of attaching skin to humanoid robots have included small anchors and hooks. However, the techniques left the skin coatings vulnerable to damage during motion. In contrast, Takeuchi’s team’s technique could theoretically be applied to any shape and could safely accommodate movement.
“During previous research on a finger-shaped robot covered in engineered skin tissue we grew in our lab, I felt the need for better adhesion between the robotic features and the subcutaneous structure of the skin,” said Takeuchi.
“By mimicking human skin-ligament structures and by using specially made V-shaped perforations in solid materials, we found a way to bind skin to complex structures. The natural flexibility of the skin and the strong method of adhesion mean the skin can move with the mechanical components of the robot without tearing or peeling away.”
The team have also suggested that the research could prove useful outside of technological applications, pointing towards medical research. They suggest that an organ on a chip is useful for drug development, and a face-on-a-chip could aid research into skin ageing, cosmetics, surgical procedures and plastic surgery.
There has been further suggestion that, by embedding sensors, the bound skin could enable humanoid robots to interact better with their environments, and with users.
“Manipulating soft, wet biological tissues during the development process is much harder than people outside the field might think. For instance, if sterility is not maintained, bacteria can enter and the tissue will die,” said Takeuchi.
“However, now that we can do this, living skin can bring a range of new abilities to robots. Self-healing is a big deal – some chemical-based materials can be made to heal themselves, but they require triggers such as heat, pressure or other signals, and they also do not proliferate like cells. Biological skin repairs minor lacerations as ours does, and nerves and other skin organs can be added for use in sensing and so on.”
Facing the future
Humanoid robotics is a developing sector more broadly, with major players – including Toyota and Tesla – investing heavily in the technology. Most designs are still prototypes, but robotic capabilities are becoming increasingly developed, and a variety of use cases are emerging across healthcare, home automation, manufacturing and beyond.
In a recent GlobalData survey, robotics was viewed as the most promising of seven major technologies, with 69% of 353 respondents from across the company’s network of B2B websites believing that it will live up to all of its promise.
Of the sector, GlobalData analyst Martina Raveni explains: “Humanoid robots are a type of robots that resemble the human body, having a torso, a head, two arms and two legs. They differentiate from the other types because they can perform tasks in ways that mimic human actions, making them suitable for complex interactions in human-centric environments.”
She points out the new advancements in artificial intelligence (AI) and machine learning (ML) processes have spurred new research and a spate of new investment. Generative AI (GenAI) specifically has catalysed interest in automation in humanoid robotics.
In the US, Tesla unveiled its AI-powered Optimus Gen2 prototype in December 2023, following Optimus Gen1 in March 2023 and Bumblebee in September 2022. Meanwhile, in China, Ubtech Robotics is currently testing Walker S for inspection work at BYD and Nio EV plants.
In Japan, Toyota has emerged as a major player in the humanoid robotic space, working on Punyo – a robot with ‘paws’, designed to carry large items in a ‘hug’. SoftBank has also invested heavily in humanoid robotic technology and has developed Pepper, an interactive robot which initiates conversation with potential customers.
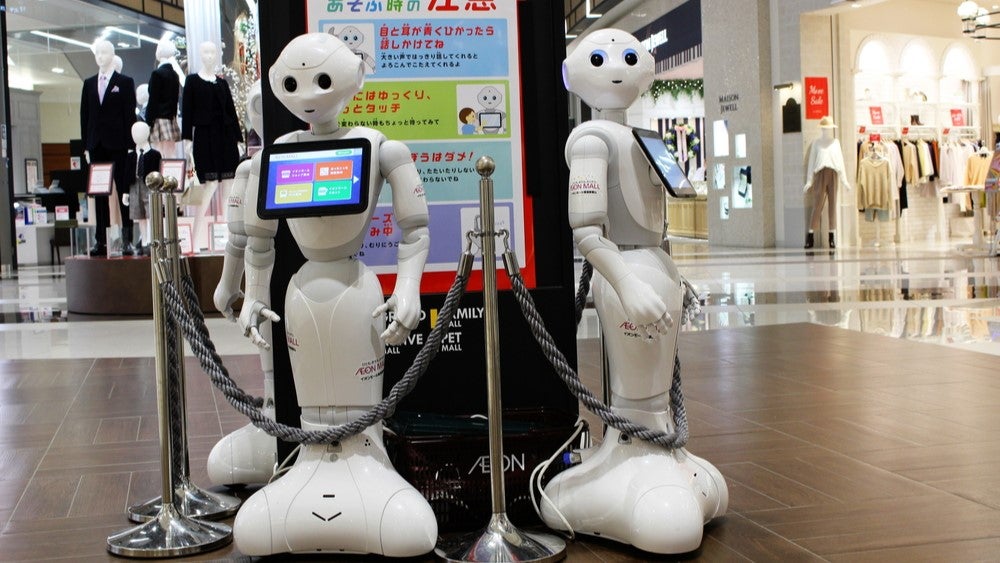
Raveni says of the as-yet-unrealised potential lying in the humanoid robotics sector: “Overall, industries are interested in investing in humanoid robots mainly to address the labour shortages, ageing population, and automation challenges. Indeed, labour cost increases and skilled worker shortages, notably in countries like China and India, drive industries to adopt robotics for competitiveness and efficiency. Robots are increasingly taking over repetitive, low-paying jobs.
“Also, demographic shifts, particularly ageing populations and declining fertility rates in developed countries, drive the demand for robots in healthcare and personal assistance roles, addressing needs like personal hygiene and meal delivery. Humanoid robots will evolve to become capable of helping meet the growing demand for elder care work.”
However, developments thus far have focused on the human-like abilities of robots, and humanoids are still distinctly non-human in appearance, lacking features such as Takeuchi’s skin. This looks set to change, as appearance and relatability become increasingly important in use cases including elder care and personal assistance roles.
These likely use cases have opened the door to new research in the aesthetic sector, and Takeuchi sees potential for further development.
“In this study, we managed to replicate human appearance to some extent by creating a face with the same surface material and structure as humans,” he said. “We identified new challenges, such as the necessity for surface wrinkles and a thicker epidermis to achieve a more humanlike appearance. We believe that creating a thicker and more realistic skin can be achieved by incorporating sweat glands, sebaceous glands, pores, blood vessels, fat and nerves.
“Of course, movement is also a crucial factor, not just the material, so another important challenge is creating humanlike expressions by integrating sophisticated actuators, or muscles, inside the robot. Creating robots that can heal themselves, sense their environment more accurately and perform tasks with humanlike dexterity is incredibly motivating.”