The circular economy is a fundamentally different approach to how products are designed, produced, and used, in which economic progress is decoupled from the consumption of Earth’s finite resources.
Manufacturers can play a key role in reshaping the supply chain and production process, to align with circular economy principles.
Manufacturing supply chains, the foundation of the global economy, are under threat following recent geopolitical uncertainties, trade conflicts, semiconductor shortages, and the Covid-19 pandemic. Economic uncertainties and rising costs have also contributed to supply chain disruption.
To protect supply chains, manufacturers can integrate circular economy principles into their business to bolster sustainability and resilience against such market shocks. This requires a fundamental shift in the way products are designed, manufactured, consumed, and disposed of. Manufacturers must embrace circular design principles, implement closed-loop systems, and collaborate across the value chain, to drive innovation, sustainability, and resilience in an increasingly resource-constrained world.
Understanding the circular production cycle
Transitioning from the traditional linear “take-make-use-dispose” approach to closed-loop systems is necessary to reduce waste and maximize resource efficiency. Manufacturers can focus on building sustainable products with durability, repairability, and recyclability in mind.
Businesses can create maximum value in the circular economy by adjusting their operations to become more sustainable. This could be achieved by improving quality control, prioritizing energy efficiency, or minimizing overproduction and waste. However, businesses keen to play a role in the circular economy must look both forward and backward. For example, manufacturers must consider where materials are sourced (and ensure such materials are sustainable) and certify products are recyclable and reusable. This may mean overhauling existing supply chains and ensuring that products are not just designed in a sustainable environment but designed with sustainability itself in mind. As such, lifecycle modeling, which involves measuring the environmental impact of a product or material throughout its lifecycle will become a key part of many companies’ ESG strategies.
How well do you really know your competitors?
Access the most comprehensive Company Profiles on the market, powered by GlobalData. Save hours of research. Gain competitive edge.
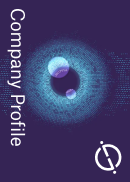
Thank you!
Your download email will arrive shortly
Not ready to buy yet? Download a free sample
We are confident about the unique quality of our Company Profiles. However, we want you to make the most beneficial decision for your business, so we offer a free sample that you can download by submitting the below form
By GlobalDataBusinesses that transition their operations to a more circular model will be best placed to benefit from policy developments on carbon pricing. Many countries, including the EU and China, are introducing emissions trading systems (ETSs) or enhancing existing ones to cover more sectors. This means that companies with higher-emission value chains will face higher costs.
The circular production lifecycle includes the following stages:
- Renewable materials: A comprehensive approach to resource efficiency underpins a truly circular economy. This includes ensuring that material inputs are renewable and recyclable. Using renewable energy sources can prevent fossil fuel stock depletion.
- Ecodesign: The circularity of a product is defined by the way it is designed. Ecodesigning a product takes the entire product lifecycle into account at the design stage. This includes the extraction of the materials used during production, the distribution and use of end-products, and their recycling and disposal.
- Sustainable manufacturing: A sustainable manufacturing journey should begin at the product design stage as it can help manufacturers make any necessary modifications and reinventions early on to help reduce waste and cost. Adopting a lifecycle approach to sustainable manufacturing will help companies measure the environmental impact of each stage involved in creating and using products.
- Use and reuse: Product users should view reuse as the first point of call after initial use. Reuse also occurs throughout any circular economy model, so it should be incorporated in every phase of a product’s production cycle and use, implicitly after any repair or refurbishment, and during sharing. Every time these steps enable a product’s continued use, it remains in the circular economy, reducing the need for new raw materials and additional energy input. Manufacturers are investing in advanced technologies to streamline remanufacturing operations and extend product lifespan.
- Recycle: Recycling involves changing waste (including unused products or goods) into a new material, product, or good. For recycling to be effective, the processes upstream must also be circular and act in sync with downstream processes. For example, not all materials are recyclable materials. The most common example of this is single-use plastics. However, greater care in ensuring materials are recyclable (or as recyclable as possible) will enable greater recyclable yields (and less waste) further downstream in the circular economy.
Manufacturers must review their existing production practices and product lifecycle to develop clear plans on how they can minimize waste and maximize resource efficiency.