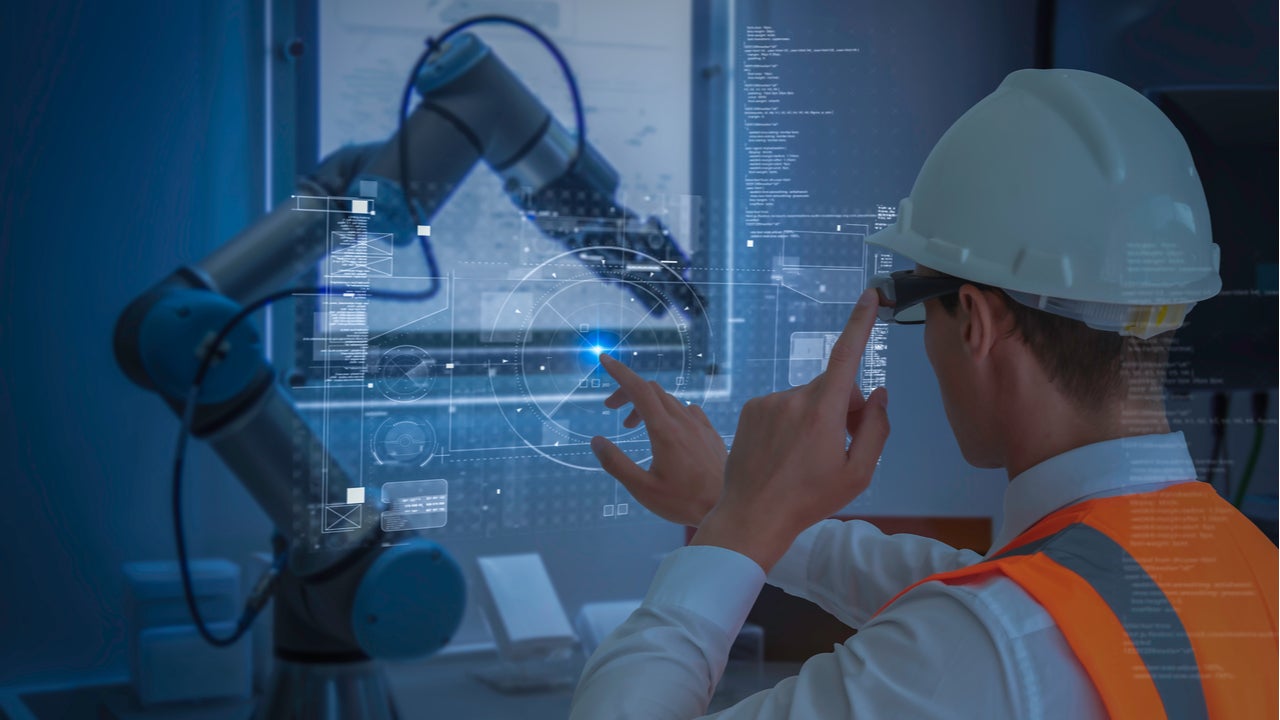
The transition from pen-and-paper-based working to digital solutions has revolutionised the way that the manufacturing industry operate. Compiling, organising and analysing data is more efficient than ever, engineering and design is increasingly advanced, and supply chain visibility has improved as every area of manufacturing can be tracked.
The widespread adoption of new and advanced smart technology across the manufacturing sector in the ongoing forth industrial revolution (industry 4.0) has levelled the playing field. In recent years, this has led to a significant increase in competitiveness across the global manufacturing sector as organisations have had to strive for the aggregation of marginal gains. To get an advantage over the competition, manufactures are looking to make improvements to all processes to ensure maximised efficiency and productivity.
The devices and software that organisations rely on to keep up in Industry 4.0 need to be developed with the future in mind. With technology continuously growing, businesses cannot afford to fall behind. Internet of Things (IoT) technology is an area that will continue to grow, with process instrumentation, sensors, monitoring and surveillance equipment becoming more advanced. A major area of advancement is Mixed Reality (MR) and Augmented Reality (AR) technology, especially when it comes to engineering. Features such as 3D mapping, virtual reality, and digital twin technology have changed the way that the industry creates and presents its designs, as well as revolutionising the way that engineers are trained.
While technology is advancing across all industries, including computers and smartphones for personal use, manufacturing industries have specific needs such as powerful processors, superfast flash storage, high-performance graphics capable of taking on the requirements of Industry 4.0 processes, and rugged casing so devices can be used on-site. While a consumer device may be used for business, it may also serve as a personal device and has not been designed specifically for commercial purposes. A rugged device is built with the rigors of industry use in mind, including IP, items built to precision standards and specs and of course, with the more reliable build and latest technology, lower failure rates and less down time.
As well as using IoT technology to increase efficiency through big data and business intelligence, the manufacturing sector is embracing digital transformation to reduce costs, improve sustainability, and acknowledge emerging skills gaps in a new era of manufacturing. Additive manufacturing / 3D printing machinery is increasingly becoming affordable to more manufacturers and has the added benefit of generating significantly less waste. Augmented Reality and Mixed Reality makes tasks such as identifying assets or accessing data much easier, and sustainable manufacturing- from reducing emissions to going paperless- is more important than ever.
Modern solutions for a modern manufacturing industry
In order to fully understand how operations can be improved, a lot of data needs to be collected from every area of the manufacturing process. Manufacturers are faced with the challenge of ascertaining the most effective method of collecting and storing data, and how this data can best be analysed in order to put improvements into place.

US Tariffs are shifting - will you react or anticipate?
Don’t let policy changes catch you off guard. Stay proactive with real-time data and expert analysis.
By GlobalDataVerdict spoke to one company that’s changing the game for manufacturers – rugged device producer, Getac – and their enterprise business development manager, James Mann, to get his take on how, despite all the changes brought about by the IoT and Industry 4.0, the best approach to ensure success in the sector is to make sure equipment failure rates are low.As one of the leading rugged computer providers, Getac offers the solution with a range of tools used to optimise manufacturing processes. Its wide array of notebook, tablet and convertible devices are designed to work in challenging environments, and its support services work closely with partners in order to build a full solution for the manufacturing sector. By sourcing a solution that provides performance, reliability and innovation from one supplier, organisations can focus their time on operations and IT teams can focus on other areas of their business.
A full range of solutions
The range of systems Getac uses include: Enterprise Resource Planning (ERP), Shop Floor Management Systems (SFMS) and Manufacturing Execution Systems (MES) software, which drive improvements in efficiency and traceability in factory operations. Furthermore, Getac supports its manufacturing customers with its own software for device management (GDMS), driver safety (GDSU, Getac Driver Safety Utility) and barcode reading (Getac Keywedge).
This range of tools offer transferable solutions that can benefit a number of industries, including food and beverage, textiles, pharmaceuticals, paper and printing, chemicals, plastics and rubber, metallurgy, and electronics. Getac’s rugged designs also ensure an extended service life, meaning continually replacing devices is a thing of the past and manufacturers can focus on carbon neutrality.
“The uptime for Getac devices is among the industry leaders due to extremely low failure rates,” Mann explains. “We own the full supply chain from research and development through to, manufacture, delivery, service and support. This allows us to guarantee the products quality, so much so that we are the only truly global rugged manufacturer that offers Accidental Damage Cover on its rugged products as standard.”
He continues: “As far as the future is concerned, I think we’ll see the steady move towards sustainable manufacturing as natural resources become more valuable and Smart Factories become the new normal. Reducing harmful emissions, harvesting solar and wind energy, installing energy-efficient lighting, equipment and machinery will be a large focus, and we have already seen a large shift towards the digitisation of processes from paper or fixed terminals to mobile devices.”