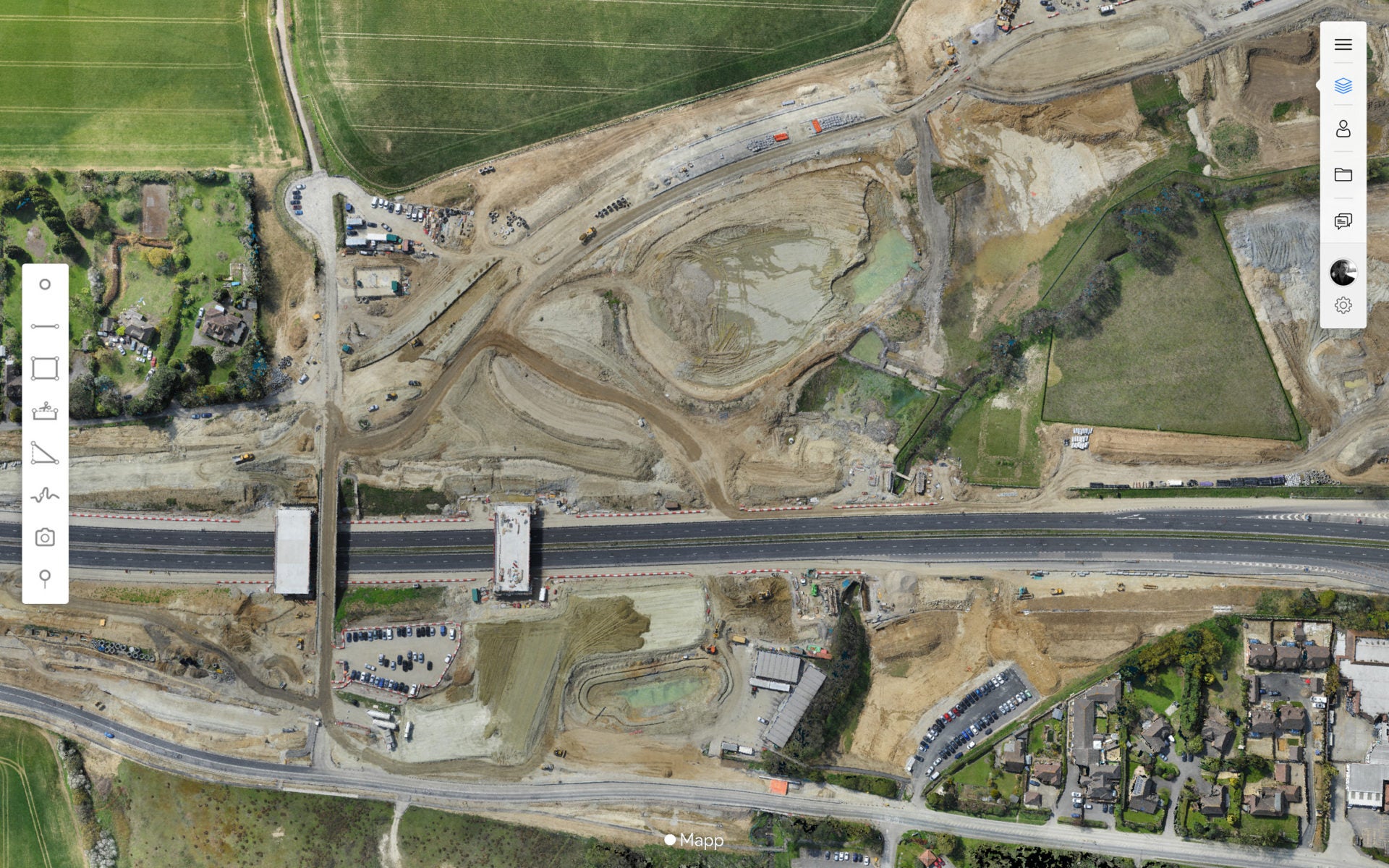
Back in 2019, industry experts were predicting that this year would be a watershed moment for digital transformation and artificial intelligence integrations in architecture, engineering, and construction (AEC). Yet no one could have predicted the rapid acceleration of digital adoption in 2020, as a result of the coronavirus pandemic and changing demand from businesses.
The pandemic – and the lockdown measures that accompanied it – expedited the need for businesses across every industry, including the AEC sector, to implement digital solutions that solve the physical limitations of on-site restrictions to ensure some level of business continuity, productivity and support the return to work.
Today, we have seen many of last year’s predictions come to fruition; digital tools are increasingly embedded into business practices and processes, AI is being used more and more to recognise patterns and predict outcomes, and the value of high quality, reliable data is finally being realised. Yet, despite all of these changes, digital transformation journeys are far from over. This is just the beginning. Change is needed now more than ever and it’s time for companies to consider how they’ll succeed and stay competitive in an increasingly unstable climate. With this in mind, the AEC industry, and the businesses operating within it, will need to create a more holistic approach to the entire asset lifecycle, ensuring technology takes prime position in their approach, supporting revenue generation and ensuring continued business success.
Digital transformation in 2020 so far
When most of the world’s countries went into lockdown, it created an immediate urgency to evaluate which processes could be digitised. Everything from work management and customer experience to processes further down the information chain, like physical data collection and analysis, needed consideration. In a world where digital is becoming increasingly relevant, businesses were adopting new solutions faster than ever before.
With the deployment of these digital tools, such as work management software, communication applications, consultation tools, and data capture technology, businesses were able to match these needs – and the results were clear. The volume of construction work undertaken on-site between March and May dropped by 2.6%, compared to the previous three months. As a result, the year on year rise in output was reduced to 3% overall. While this is still a reduction, digital transformation prevented the output from being smaller, as well as far greater setbacks in construction projects that were anticipated during this period. In fact, at a time reducing costs was a top priority and the delay of investments was being discussed in relation to facilities, operations, and the workforce, technology was able to save significant cuts. For the 81% of CFOs considering cost reductions in response to the crisis, digital transformation may have helped reduce some of the pressure felt over the past few months.
And now that we are coming out of lockdown, we are already seeing a sharp increase in construction output as sites reopen. The IHS Markit/CIPS construction purchasing managers’ index (PMI) read 55.3 in June. Given that it read just 28.9 a month earlier in May, this statistic is significant. Much of this could be attributed to the digital technologies adopted during lockdown that have enabled work to continue, and new initiatives kick off within these projects.
How well do you really know your competitors?
Access the most comprehensive Company Profiles on the market, powered by GlobalData. Save hours of research. Gain competitive edge.
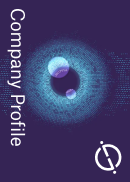
Thank you!
Your download email will arrive shortly
Not ready to buy yet? Download a free sample
We are confident about the unique quality of our Company Profiles. However, we want you to make the most beneficial decision for your business, so we offer a free sample that you can download by submitting the below form
By GlobalDataYet with all these projects resuming or starting in a post-Covid-19 world, it is pressing to ask what changes we can expect in the sector.
What needs to happen next?
While many companies are starting to find their way through the crisis, they now have to think about the future and what will help them remain successful in the long term. One immediate concern is the new balance being struck between previous ways of working and the new digital technologies and assets available. AEC businesses must be flexible and open to change, as they adapt to a new normal, in order to maintain focus on revenue generation and overall business success. Digital twin technology is a key solution for AEC businesses, to survey their infrastructure sites faster without ever having to go onsite, as well as visualising and interacting with topographical and design data. This will enable teams to recognise patterns, predict outcomes and drive up revenue generation in unprecedented ways.
Today, capturing data in construction goes far beyond paperwork and spreadsheets, and the benefits are endless if tools are utilised in the right way. In order to effectively use the information being collected, businesses need to ensure they have the correct systems in place to not only collect and structure the information but additionally, translate it into something understandable that can be used in a meaningful way.
However with a lack of industry standards to help transfer information between projects, companies and suppliers, there is a limit to how useful some of today’s systems can be. Across the industry, there is a need to break down silos, gather new and better data, and enable the interlocking of data and projects. For the industry to mature collectively, progress cannot be made individually but needs to be shared widely. This will open up the digital market by improving understanding, productivity, costs, and overall support sustainability.
As well as Boris’s £5 billion infrastructure investment plan, The Department for Transport in fact recently unveiled its Transport Infrastructure Efficiency Strategy Living Lab initiative, involving an investment of more than £16 million in new tools and data systems, with the aim to increase efficiency in projects in order to free up public money. Both of these initiatives will kick start the industry again, but digital infrastructure will be paramount to success, and meet targets in place under the ‘Digital Built Britain’ programme, which champions the digital revolution in the built environment.
Digital transformation in construction: Data is key
If the industry were to aim for just one thing, trusted data should be top of the list. It is the key that will unlock digital transformation and – if realised – will provide a single source of truth. Data alone won’t drive success, but the technology and the analytics that are built around this data that enables actions that will support better decision making and the industry as it recovers. AI, analytics and collaboration will create trusted data, where companies can now work on projects with any number of workers from any number of places, remotely and in the faith that they are all seeing the same accurate representation of the real world.
With all of these possibilities, the potential risks need to be considered too. With the rise of data usage across infrastructure sites and a maturing approach to digital, we need to pay more attention to security and privacy. Data can open up risks, and as an industry, we need to ensure we protect our businesses, people, process and our environment, particularly in these uncertain times.
And for those that haven’t undertaken some form of transformation during this period, now is the time to rethink how your company operates and look to accelerate your adoption of digital technologies. Companies need to reimagine their business models, and digitally transform by accelerating their adoption of technologies which increase efficiencies, while safeguarding the health and safety of employees, and upskilling them. This is a lot to consider and many may struggle in the short term, but the benefits in the long term are limitless. The future is unpredictable, but by better using digital tools we can make better-informed decisions which can open up a world of opportunities.
James Dean is the co-founder and CEO of Sensat, a UK startup that creates software to map digital twins of real-world assets.
Read more: CTO Talk: Q&A with Sensat’s Lorenzo Alberton