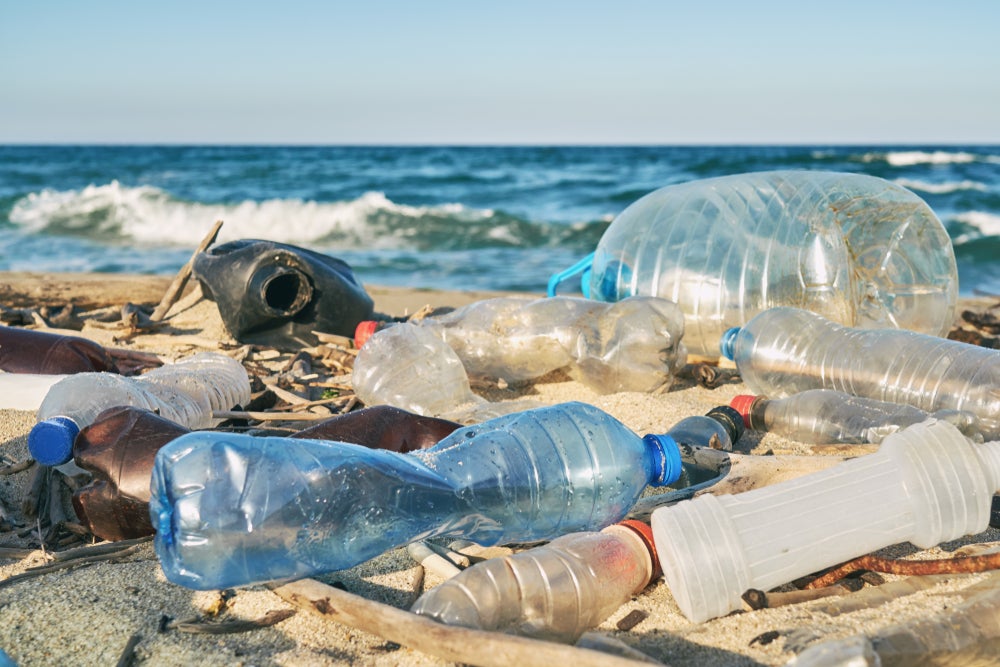
A bio-plastics partnership has developed the chemistry behind a plant-based fire-suppressant building material that could have helped prevent the Grenfell disaster in London in June 2017.
Grenfell Tower is a block of flats in North Kensington, London that suffered a major fire and resulted in 72 deaths. A public inquiry into the fire is still going on, but the building’s exterior cladding is thought to have contributed to the quick spread of the fire. The petrochemical foam insulation behind the cladding could also have contributed to the toxicity of the smoke.
The plant basis of Teysha Technologies’ plastics and the company’s ‘tuneable’ technology could produce a self-extinguishing foam insulation that might prevent a disaster like Grenfell happening in new buildings.
The plastics solution
Teysha also hopes to help with other aspects of the plastics problem – the widespread concern over plastic waste and microplastics in the environment and in the sea. Microplastics are the tiny particles of less than 5mm created in the breakdown of some plastics.
The technology uses natural and cost-effective sources, like agricultural waste and other biomass, to build the polymers. It also promises ‘hydrolytic’ breakdown where the materials are broken down by water to their starting molecules.
It is a whole lifecycle approach to plastic products. “We build up from these natural products and then design it so that when it breaks down it goes all the way back down to those same natural products. So as it breaks down in the environment, it’s not leaching some of this nasty stuff like the petrochemicals do and also not persisting for thousands of years,” says Dr Ashlee Jahnke, Teysha Technologies’ head of research and development.
How well do you really know your competitors?
Access the most comprehensive Company Profiles on the market, powered by GlobalData. Save hours of research. Gain competitive edge.
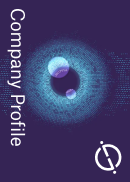
Thank you!
Your download email will arrive shortly
Not ready to buy yet? Download a free sample
We are confident about the unique quality of our Company Profiles. However, we want you to make the most beneficial decision for your business, so we offer a free sample that you can download by submitting the below form
By GlobalData“Ten years ago the research could have produced these types of plastics, but no one’s going to pay $100 for their water bottle to be thrown out, so the real leap is being able to apply our methodologies to low-cost agricultural waste.”
The plastics problem
Jahnke describes the problem with traditional plastic: “Most plastic is derived from petrochemicals coming from oil and for years and years, plastics engineers and chemists always designed their plastics for a specific function or purpose – that was really the focus. ‘Can we make a plastic to do this specific job’, whether it was this packaging or whatever it might be, without a lot of thought of the sourcing of the starting materials or the end of life and where these things might end up.
“That’s how we’ve created this problem, especially with single-use, and when they get into the environment they can persist for thousands of years. There’s no mechanism for those to break down and go away, and in fact what we’re seeing is that even some of those that break down are ending up as microplastics, these tiny little pieces, and these are ending up on your dinner plate, we’re finding them in our food chain now.”
The chemistry of polymers
The solution is ‘tuneable’ biopolymers or plastics that have specific properties or functionalities to do the job of the product effectively and not persist in the environment after they have been used and discarded.
Jahnke says, “So chemistry is all about installing the functionalities that you need on molecules to do the reactions later. The focus is on how you install these functionalities to biomass materials. We’re looking at ways to breakdown those materials and install the functionalities we need.”
Explaining a polymer, Jahnke says, “Most new plastic is just one polymer. So in a polymer chain, you take one little repeat unit, like one bead in a necklace, and you put a bunch together to get a long string. You take whatever your ingredients and combine them and make a big giant molecule and that’s what you call a polymer or plastic.”
Tuning the properties of the biopolymer
“If you want different applications you can make those chains short or long, that’ll change the properties, you can mix it with some additives, things like that, but it’s based on the properties of the specific polymer you make,” explains Jahnke.
“What’s unique is the way we can modify certain natural properties and the way we combine them so that we can ‘tune’ the properties of the end material. If you need packaging that’s very rigid to protect something, we do one formula, if you need something soft and squishy we do a different one and it’s all under the same technology platform.”
The plastic that already exists in buildings, packaging and everywhere around us remains a problem, in terms of its risks and disposal. And there are big economic questions around how we replace these, long term solutions and government policies on the use of plastics. Teysha Technologies offer a way to step out of the plastics dependency in a more renewable and environmentally friendly way.