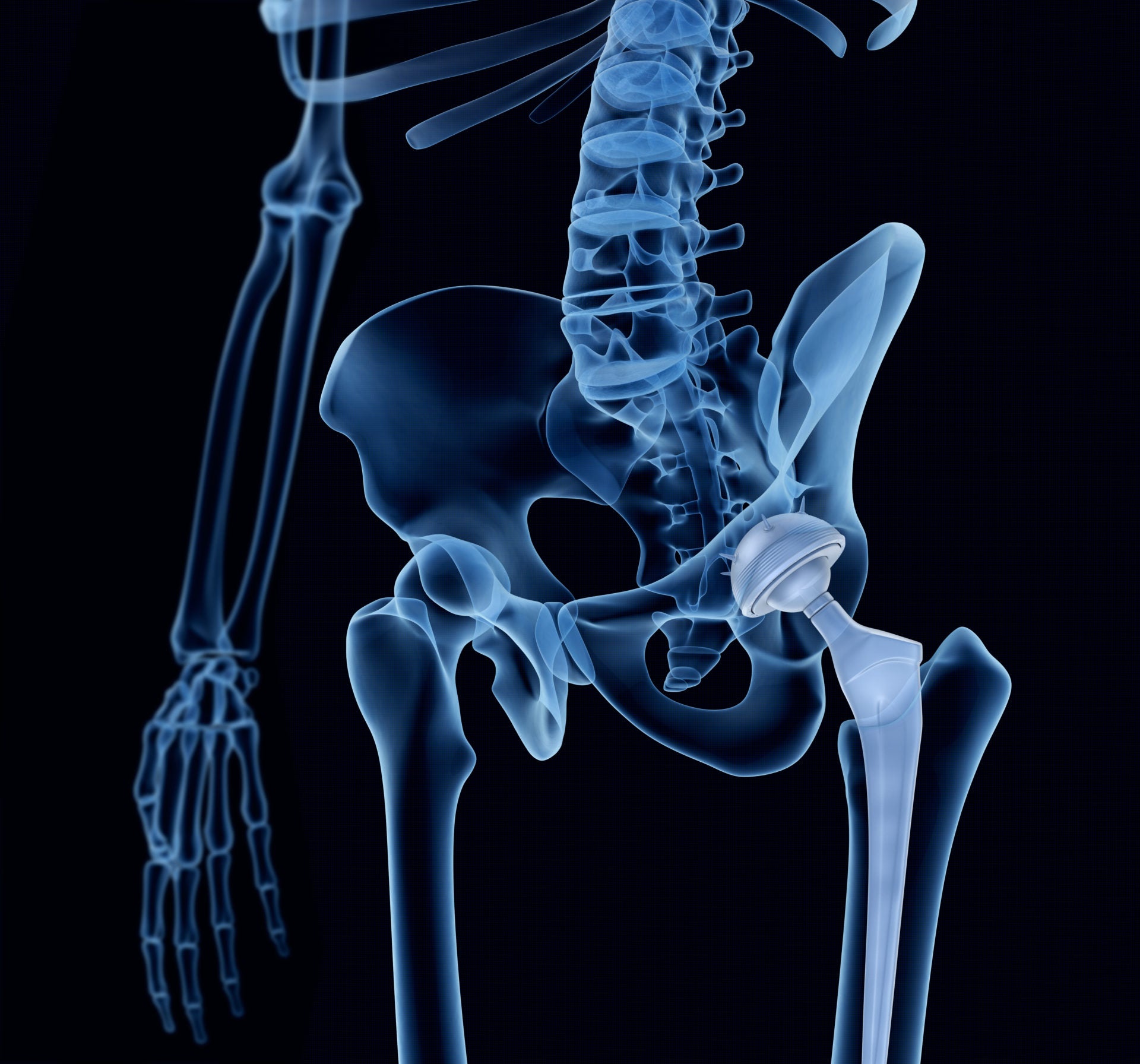
Scientists from German research organisation Fraunhofer have devised a process to make 3D printed bones that are more realistic and less likely to be rejected by the human body than previous versions.
The 3D printed bones can be made with different densities throughout the structure, much like real human bones.
This will allow doctors to meet the specific needs of individual patients, as well as making the implant more precisely fitting and more stable.
“This development by our project partners from Maastricht University makes it possible to individually vary the stability inside the implant,” said Dr Thomas Neubert, manager of the EU project at Fraunhofer IST.
“Like natural bones, implants can now have areas with different strengths.”
The Fraunhofer Surface Engineering and Thin Films IST team, in collaboration with European research partners, also improved the bonding process between the body’s bone-forming cells and the plastic implant.
To do this, they used a plasma jet to blow a cold jet of plasma containing reactive groups directly onto the printed layers.
These reactive groups assist the bonding process by ensuring amino groups find suitable organic material to adhere to.
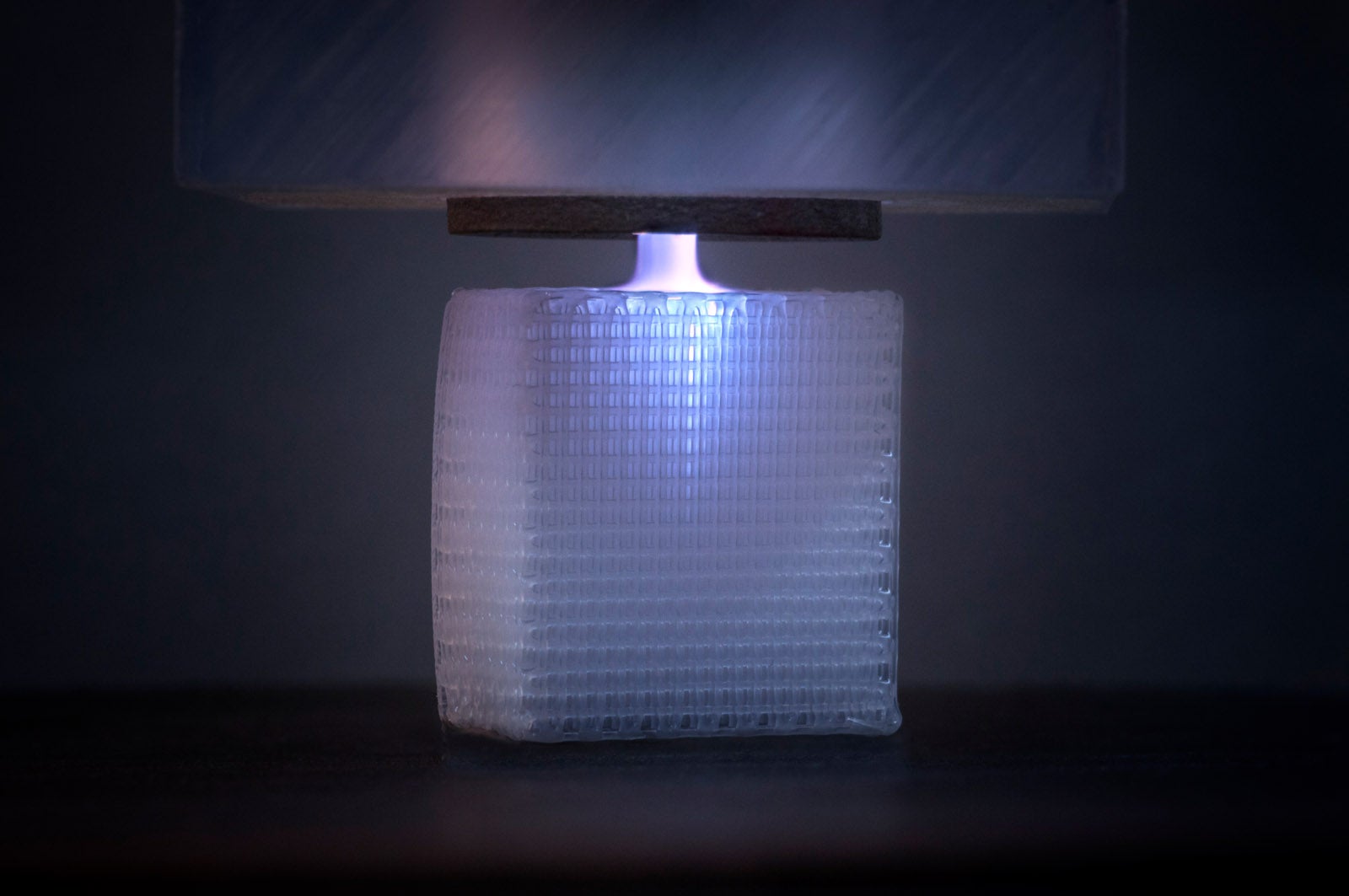
The coating process is carried out at the same time as the 3D printed bone is created. This makes it environmentally friendly because it doesn’t require chemical pre-treatment with solvents, as well as cost-effective.
“Our goal is for the bone cells to grow into the synthetic structure as quickly as possible and finally replacing the implant, which is broken down gradually by the body’s own enzymes,” explained Dr Jochen Borris head of the Life Science and Ecology business unit at Fraunhofer IST.
3D printed bones with greater stability
The stability of the implant is improved in specified areas by adding a special filler to the copolymer framework of the implant, which is modelled on natural bone.
By adding a higher concentration of the filler, the researchers can increase the bone density in that particular area.
“With our method, we’re able to control the shape, porosity, mechanical stability and biomechanical characteristics well and vary them within the implants,” explained Borris.
“This means that we can produce areas with different strengths or porosities, which can also be coated with various functional groups.”
One day, doctors may be able to x-ray a patient and send the data to a medical print shop for fabrication. But before then, the team needs to refine the technique with a view to bringing it onto the market.
“We’re currently working on simplifying the process and making it more stable,” said Borris.
“To be able to further pursue development and carry out clinical studies, we’re on the search for industrial partners.”
Read more: How close are 3D printed organs to reality?